The Essential Guide to Plastic Mold Making: A Comprehensive Overview
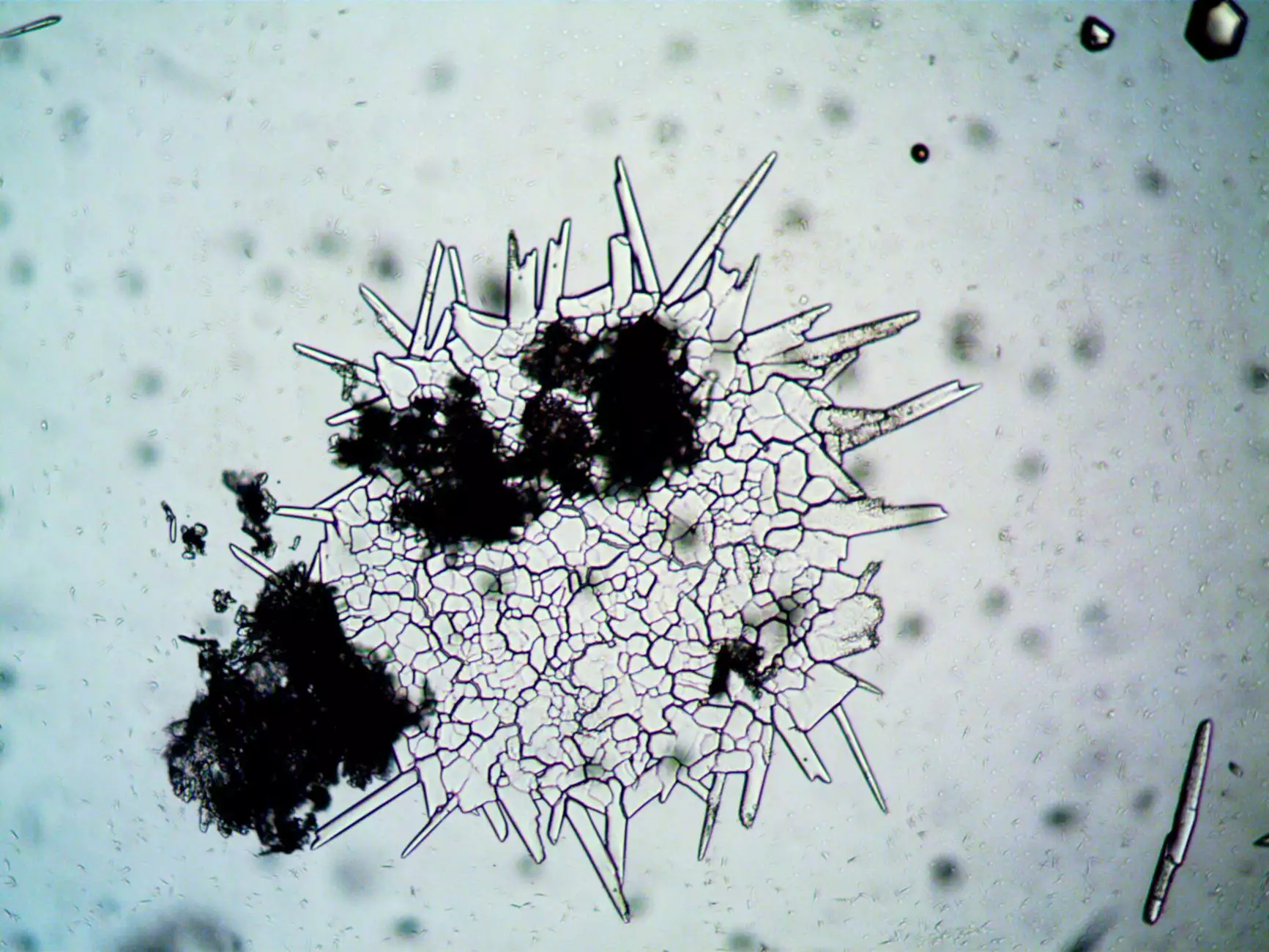
The field of plastic mold making is a cornerstone of modern manufacturing, offering extensive applications across various industries. As businesses continuously seek efficiency and cost-effectiveness, understanding the nuances of this craft is crucial. In this article, we delve deep into the world of plastic mold makers, highlighting the significance of this industry, its methodologies, and why countries like China are leading the charge with companies like Hanking Mould.
What is Plastic Mold Making?
Plastic mold making is the process of designing and fabricating molds that produce plastic parts through various manufacturing techniques. This involves creating a mold—typically composed of metal—into which plastic is injected, heated, and cooled to create the desired shape. These molds are significant not only for their utility but also for the precision and durability they provide in manufacturing.
Types of Plastic Mold Making Techniques
There are several common techniques utilized in plastic mold making, including:
- Injection Molding: This is the most prevalent method. Plastic resin is melted and injected into a mold.
- Blow Molding: This technique creates hollow plastic parts by inflating hot plastic into a mold.
- Rotational Molding: In this method, plastic powder is heated and rotated in a mold to create large, hollow parts.
Understanding the Role of a Plastic Mold Maker
A plastic mold maker plays a pivotal role in the manufacturing process, responsible for designing, crafting, and maintaining molds that produce quality plastic parts. From conceptualization to production, a skilled plastic mold maker utilizes various tools such as CAD software, CNC machines, and advanced design techniques to ensure precision and reliability.
Key Qualities of a Successful Plastic Mold Maker
To excel in this industry, a plastic mold maker should possess several key qualities:
- Attention to Detail: Precision is paramount; even minor errors can lead to significant defects in production.
- Technical Proficiency: Strong computer-aided design skills allow mold makers to create intricate designs accurately.
- Problem-Solving Skills: The ability to diagnose and rectify issues efficiently is essential to maintaining production timelines.
The Manufacturing Process of Plastic Molds
The mold-making process is intricate and involves several critical steps:
1. Design
The initial phase involves creating a design that meets the specifications of the product. This often includes 3D modeling and prototyping.
2. Material Selection
Choosing the right materials is crucial for mold durability. Common materials include steel and aluminum, known for their resilience and ability to withstand high temperatures.
3. Machining
This is where the actual mold is created. Using CNC machines, the latter is carved out of the selected material as per the design specifications.
4. Assembly
After machining, the components of the mold are meticulously assembled to ensure that all parts fit perfectly.
5. Testing
Quality testing of the mold ensures that it meets production standards. This often includes trial runs where plastic is injected into the mold.
6. Production
Once the mold passes testing, it is shipped to production lines for the mass production of plastic parts.
Advantages of Working with a Leading Plastic Injection Mould Manufacturer
Choosing a reputable plastic injection mould manufacturer such as Hanking Mould carries numerous advantages:
- Quality Assurance: Established manufacturers adhere to strict quality control measures, ensuring that the molds produced are of the highest caliber.
- Faster Turnaround: With experience, leading companies can produce molds more swiftly, reducing time to market for products.
- Advanced Technology: Investing in the latest technology allows manufacturers to provide innovative solutions and maintain a competitive edge.
The Importance of Material Selection in Plastic Mold Making
Material choice can impact not only the mold's durability but also the quality of the final product. The common materials used include:
- Steel: Optimal for high-volume production due to its strength and durability.
- Aluminum: A lighter alternative, ideal for low to moderate production volumes.
- Specialty Materials: Custom alloys or plastics designed for specific applications.
Sustainability in Plastic Mold Making
In an era where environmental impact is a serious concern, the plastic mold making industry is evolving. Manufacturers are focusing on creating sustainable processes:
- Recyclable Materials: Utilizing plastics that can be recycled addressing environmental concerns.
- Energy Efficiency: Investing in energy-efficient machinery reduces overall carbon footprints.
- Waste Reduction: Strategies to minimize waste during the manufacturing process contribute to sustainability.
Case Studies: Successful Applications of Plastic Mold Making
1. Automotive Industry
The automotive industry is a significant consumer of plastic parts, exemplifying the importance of quality molds. Manufacturers rely on precision to create components that are lightweight yet durable, enhancing vehicle performance.
2. Consumer Electronics
In the fast-paced world of consumer electronics, plastic parts are integral to product design and functionality. Molds must be produced rapidly without sacrificing quality to keep up with technological advancements.
Future Trends in Plastic Mold Making
As technology advances, the plastic mold making industry is poised for significant changes. Anticipated trends include:
- Increased Automation: Automating processes from design to manufacturing enhances efficiency.
- 3D Printing: The growing adoption of 3D printing techniques is revolutionizing mold production, permitting rapid prototyping and customization.
- Smart Manufacturing: Integration of IoT and AI will lead to smarter factories with predictive maintenance and real-time production monitoring.
Conclusion
Understanding the intricacies of plastic mold making is essential for anyone involved in manufacturing today. As we have explored, the role of the plastic mold maker is indispensable in transforming concepts into tangible products. With companies like Hanking Mould leading in quality and innovation, the future of plastic mold making looks promising. By prioritizing quality, investing in technology, and focusing on sustainability, businesses can ensure they remain at the forefront of this dynamic industry.
As you venture further into the world of plastic mold making, remember that staying informed and adaptable is key to thriving in this competitive landscape. Whether you are a manufacturer, a supplier, or a client, the insights provided here will equip you for success in the evolving market of plastic injection moulds.